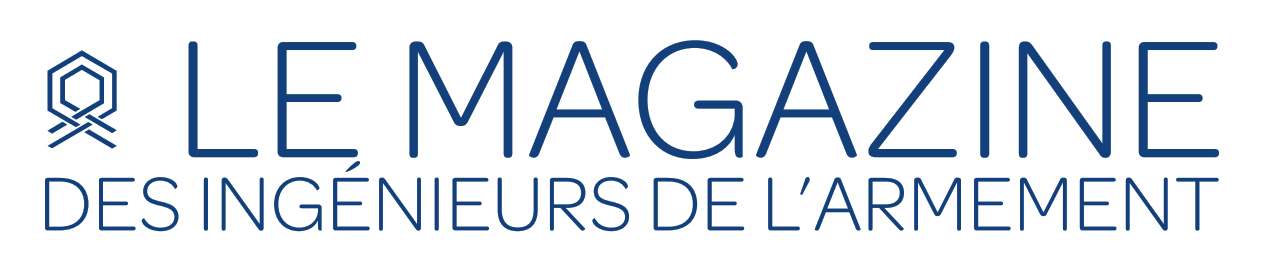
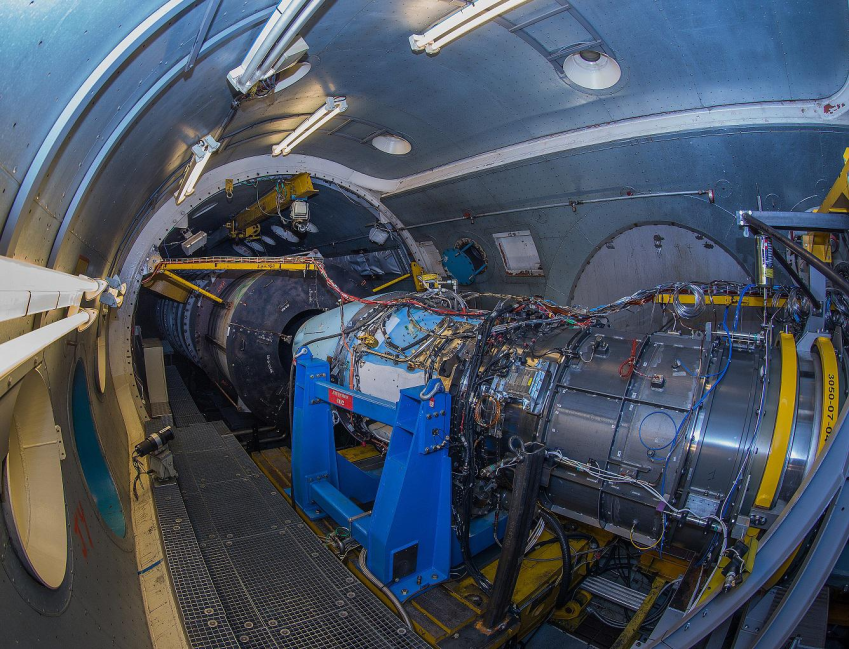
OPTIMISER L’IMPRÉVISIBLE
OU COMMENT OPTIMISER UNE PRODUCTION PAR NATURE NON RÉPÉTITIVE ET SOUMISE À DE NOMBREUX ALÉAS
La production d’essais se distingue de la production en chaîne par la grande variabilité des problématiques rencontrées : chaque essai est unique, et chaque essai réserve son lot de surprises… Optimiser un processus en perpétuelle transformation est le défi quotidien des centres d’essais de la DGA comme DGA Essais Propulseurs.
Mardi 16h, Outlook sonne : « Le client a fini d’exploiter les résultats des essais de la semaine dernière. Le moteur ne s’est pas comporté comme prévu, il veut revoir les points d’essais de la semaine prochaine. La campagne sera probablement prolongée de 2 semaines, j’attends une confirmation. » OK… Ça, c’est si tout se passe bien. Sinon, c’est endoscopie du moteur, voire dépose anticipée.
Le monde des essais réserve régulièrement son lot de surprises. C’est ce qui fait son charme, mais c’est aussi un casse-tête pour celui qui cherche à organiser sa production. Surtout dans un centre comme DGA Essais Propulseurs (DGA EP), où les différents essais sont intimement dépendants les uns des autres car ils utilisent des ressources communes. Pour les essais de turbomachines en altitude simulée, les caissons d’essais sont reliés en amont et en aval à des installations dites d’« atmosphérisation ». Cela consiste en des réseaux de collecteurs d’air, des compresseurs, des sécheurs, des réfrigérants, etc… qui permettent de reproduire, en caisson, les conditions atmosphériques auxquelles sont soumises les turbomachines en altitude, que ce soit en terme de pression, de température et d’hygrométrie. Or ces moyens sont communs à tous les caissons d’essais. Modifier les points d’essais sur un caisson oblige à reconfigurer le réseau et peut, si l’on n’y prend pas garde, rendre impossible la réalisation d’un autre essai dans un caisson voisin.
Le retour aux fondamentaux
Comment s’en sortir ? En ayant bien à l’esprit des concepts de base, qui ont fait leurs preuves. Un processus est régi par les hommes, les outils et les méthodes. Ces trois piliers sont interdépendants et sont tous nécessaires : l’homme sait bien s’adapter aux imprévus mais il est intrinsèquement faillible, l’outil permet de gagner en productivité et est plus fiable mais il ne fait qu’exécuter un algorithme, la méthode permet d’organiser le processus mais ne produit rien en soi. La réussite passera par le bon équilibre entre ces trois piliers, et de bonnes interactions entre eux.
Les principes du lean management ne sont pas récents mais restent complétement d’actualités. Il faut, comme toute production, s’attacher à supprimer les irritants. D’abord le « muda » : le gaspillage inutile de ressources. Cela se traduit par exemple à DGA EP par des installations d’atmosphérisation électriques qui, outre leur intérêt en matière de protection de l’environnement, ont l’immense avantage d’être mises en fonctionnement dans des délais beaucoup plus courts que leurs aînées thermiques. Cela passe aussi par le choix au plus juste de la machine d’alimentation ou d’extraction d’air nécessaire pour l’essai du jour (avec parfois un facteur 10 dans les coûts de production). Ensuite le « muri » : l’excès. Il s’agit de simplifier tout ce qui peut l’être. Cela va des procédures, formulaires, parapheurs, etc… jusqu’à la simplification du travail de l’opérateur. A DGA EP par exemple, l’intégration des turbomoteurs sur leur bâti d’essais est réalisée en atelier lorsque c’est possible, avant de transporter ensuite l’ensemble vers le caisson d’essais. Pour que tout ceci soit le plus efficace possible, il ne faut pas oublier le « kaizen », c’est-à-dire que ce sont les agents de terrain qui sont le plus à même d’identifier quelles sont les améliorations envisageables les plus pertinentes. Ce sont donc eux qui doivent être à l’origine de ces améliorations. D’autres méthodes existent, le 5S, le six sigma, etc… toutes sont importantes à avoir à l’esprit car elles permettent d’épurer le processus et de se concentrer sur l’essentiel.
Réseau d'alimentation en air des caissons d'altitude simulée R3 et R4 de DGA Essais Propulseurs
Réactivité, souplesse, adaptabilité
Chaque processus industriel doit mettre en oeuvre des principes d’amélioration continue, sur le modèle du « plan », « do », « check », « act ». Mais pour pouvoir s’adapter en permanence aux aléas inhérents aux essais, il est indispensable de raccourcir cette boucle décisionnelle. La révolution numérique permet aujourd’hui d’envisager la mise en place d’outils prédictifs inenvisageables il y a dix ans. Ces outils permettront, d’une part, de mettre en évidence les conflits potentiels de ressources matérielles et humaines (projet planification), et, d’autre part, de prédire le comportement aérothermique des installations d’« atmosphérisation », c’est à-dire les installations qui permettent de reproduire au sol les conditions atmosphériques régnant en altitude (projet SIMATMOS). La principale difficulté, pour le premier projet, est de savoir prendre en compte des contraintes multiples, apparaissant sur des plans différents : disponibilité et compétence des ressources humaines, occupation des caissons, disponibilité de réseaux qui peuvent se croiser, mises en sécurité des personnels qui peuvent intervenir pour maintenance sur une partie du réseau alors que l’autre est en fonctionnement, pertes de charge en pression et température, maîtrise de la consommation électrique, etc… Ce projet, encore embryonnaire, sera mené selon les principes de l’ingénierie système.
Pilotage en temps réel des réseaux et des machines d'alimentation et d'extraction d’air
SIMATMOS
Le projet SIMATMOS vise à développer un outil de simulation prédictive du fonctionnement des installations d’atmosphérisation. Un tel outil permettra de tester numériquement de nouvelles configurations moyens d’alimentation en air / caisson d’essais / réseaux / moyens d’extraction d’air afin d’en simuler les effets et les contraintes qu’elles induisent sur les installations du centre. Il s’agit donc in fine d’un puissant outil d'aide à la décision puisqu’on pourra ainsi comparer plusieurs scenarii et visualiser sans risques et sans coûts leurs prérequis et leurs conséquences. Combiné à une interface homme-machine proche de celles présentes dans les installations d’essais, cet outil permettra aussi de former les opérateurs à moindre coût, et d’entretenir leurs compétences. Le recours à la simulation permettra aussi de former plus efficacement les opérateurs à la gestion des aléas (pannes).
Évidemment, la qualité d’un tel outil dépend directement de la précision des modèles physiques employés ainsi que de leur représentativité vis-à-vis des comportements réels en essais. Ce dernier point, qui constitue le point dur majeur du projet, fait l’objet d’une attention particulière. Les premiers modèles, construits à partir des données physiques de nos matériels, seront ainsi recalés selon une logique précise à l’aide de bases de données complètes de mesures réalisées dans nos installations depuis de nombreuses années.
Comme mentionné précédemment, l’outil seul, aussi puissant soit-il, est insuffisant : il doit s'inscrire dans le triptyque agent – méthode – outil. Dans le cas de SIMATMOS, cela signifie concevoir, autour de l'outil, les méthodes d’utilisation, d'administration et d'amélioration de l'outil par les agents. Car cet outil doit être vivant, améliorable et adaptable, au gré des évolutions physiques de nos matériels mais aussi des attentes des utilisateurs. C'est cet ensemble qui constitue au final la solution qui répond au besoin, pas l’outil seul. Le projet est mené depuis le départ en utilisant la logique et les processus de l’ingénierie système, ce qui assure une bonne prise en compte de l’environnement du produit et une approche cycle de vie dans la conception de la solution ainsi qu’une définition du besoin et des performances de l'outil aussi précises que possible tout en se limitant au juste besoin.
Optimiser l’imprévisible, c’est donc avant tout un ensemble cohérent de méthodes souples et claires, d’outils prédictifs d’aide à la décision et une culture de la souplesse et de la réactivité. Mais surtout une capacité à s’adapter en permanence, et pour cela des outils maîtrisés en interne et avec une architecture ouverte sont indispensables.
Auteurs
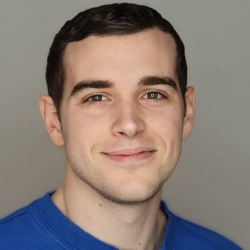
Aucun commentaire
Vous devez être connecté pour laisser un commentaire. Connectez-vous.