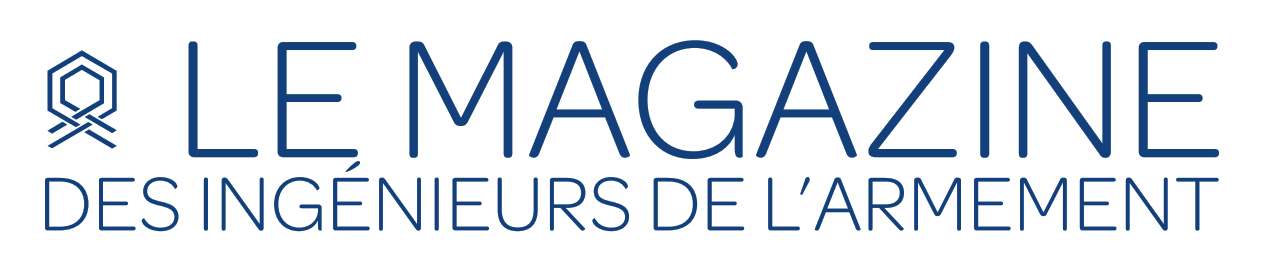
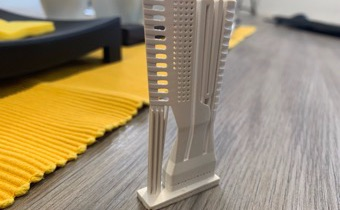
Fail Fast et conception d'aubes de turbine
Que peut apporter la fabrication additive dans des procédés ancestraux et empiriques ?
Placer un glaçon dans un four thermostat 8 et faire en sorte qu’il ne fonde pas ? C’est le défi que doivent relever les ingénieurs qui conçoivent les aubes de turbine haute pression des moteurs d’avion.
Le 7 février 2019, le magazine Aviation Week écrivait : « At least nine countries can make nuclear bombs, but just two— the U.S. and UK—can make single-crystal turbine blades for modern aeroengines. ». Hasard du calendrier et n’en déplaise à nos amis anglo-saxons, Safran inaugurait la veille la nouvelle plateforme de recherche sur les aubes de turbines avancées pour moteur d’avion et d’hélicoptère, en présence de Mme Florence Parly, ministre des Armées, et Mme Ursula Von den Leyen, ministre de la défense allemande, rappel particulièrement opportun de la compétence française de longue date en matière de turbine haute pression, avec son application la plus symbolique : le M88, le moteur du Rafale.
Le procédé de fonderie de nos jours. Source : Safran
La turbine, au cœur du moteur
La turbine haute pression est en effet au cœur du moteur : il s’agit du premier élément en rotation placé derrière la chambre de combustion. Ayant pour fonction d’entraîner le compresseur, les aubes de turbine doivent survivre à des conditions
infernales : rotation à plusieurs dizaines de milliers de tours par minute et température de l’air supérieure à 1600°C, largement au-delà de la température de fusion de l’alliage qui les compose. Pour qu’elles ne fondent pas, de l’air plus froid, prélevé sur le compresseur, circule en leur sein à travers un réseau complexe de minuscules canaux de refroidissement internes. Pour optimiser au maximum les propriétés thermomécaniques du matériau, chaque aube de la turbine haute pression a la particularité d’être monocristalline : elle est métallurgiquement constituée d’un et un seul cristal, à l’image d’un diamant.
La conception et la réalisation de ces circuits de refroidissement est un savoir-faire industriel propre à chaque grand acteur de la propulsion aéronautique, et rigoureusement préservé tant cette fonction est critique pour le bon fonctionnement de la turbomachine. Le rendement global du moteur dépend en effet directement de la performance de la turbine : l’aubage doit être aérodynamiquement optimal, mais aussi suffisamment robuste pour conserver une durée de vie et donc un coût opérationnel satisfaisant. Chaque aubage turbine haute pression est ainsi le résultat d’un compromis longuement recherché par les ingénieurs, qui pour concrétiser leur création ont recours à un procédé vieux de plus de 5000 ans : la fonderie à cire perdue.
Le procédé de fonderie, une histoire de noyau
La fonderie à cire perdue existe depuis l’antiquité pour réaliser des formes complexes, de manière précise et répétable. C’est le procédé de choix pour les turbines haute pression, notamment lorsqu’elles nécessitent d’être creuses pour être refroidies.
Les canaux de refroidissement des aubes sont réalisés dès le début du procédé grâce à l’utilisation d’une empreinte « positive » des circuits, nommée le noyau céramique. Le métal sera coulé autour de ce noyau qui sera ensuite dissous dans un bain chimique, laissant en creux le « négatif » de l’empreinte des canaux de refroidissement dans la géométrie métallique désirée. |
Le savoir-faire de l’industriel est alors non seulement de concevoir et calculer ces circuits pour obtenir la circulation d’air froid désirée, mais également de les réaliser dans un matériau céramique capable de prendre des formes très complexes, tout en résistant à toute la suite du procédé de fonderie, incluant notamment la coulée métallique avec du métal en fusion à plus de 1200 °C.
Il s’agit donc d’un processus complexe nécessitant de très nombreuses étapes, comportant par ailleurs un taux de rebut très élevé par rapport à d’autres procédés industriels : comme le fait remarquer Aviation Week dans son article, entre 10 et 20% de la production est mise de côté, ce qui la rend très coûteuse.
Cependant, pour rester compétitive, cette industrie n’aura d’autre choix que de s’adapter aux enjeux de demain : alors que l’amélioration du rendement et de la performance des moteurs passe par l’augmentation de plus de 250°C de la température de fonctionnement, les aubages devront être refroidis de plus en plus efficacement tout en restant industrialisables.
Pour y parvenir, les industriels continuent à innover dans le carcan du procédé de fonderie actuel même si, ces dernières années, un procédé de choix a atteint un niveau de maturité suffisant pour espérer en sortir : la fabrication additive.
La fabrication additive, un catalyseur de mutations
Pour des raisons de répétabilité, les industriels privilégient l’utilisation de moules pour réaliser les géométries de noyau. L’inconvénient est cependant d’imposer une direction privilégiée sur la géométrie selon l’axe de démoulage, contraignant d’autant la liberté de conception. L’utilisation de la fabrication additive céramique pour réaliser le noyau offre une plus grande liberté aux concepteurs, en rendant fabricables des circuits d’air plus complexes pour améliorer la performance thermomécanique des futurs aubages. Mais le procédé d’impression 3D n’est pas exempt de contraintes : l’enjeu est de réussir à l’intégrer au sein de la gamme de fabrication. Encore très empirique, chaque modification d’un paramètre du processus nécessite un plan d’expérience pour être validée, avec une longue période de mise au point. La fabrication additive est cependant capable de tirer son épingle du jeu grâce à la grande souplesse qu’elle autorise : là où la fabrication et la qualification industrielle d’un moule de fonderie prend plusieurs mois et suppose que la définition de la pièce à réaliser soit figée, la fabrication additive s’affranchit de ce fonctionnement séquentiel et permet de mener la conception et l’industrialisation de la pièce en parallèle, avec des allers-retours rapides entre les deux disciplines.
Le prototypage rapide par impression plastique permet par exemple de rapidement tester des configurations de noyau pour identifier le meilleur concept, et de réaliser une myriade d’artifices de production pour améliorer la répétabilité du procédé. Les premières impressions en céramique peuvent ensuite être réalisées et permettent de s’insérer dans le procédé global, tout en conservant de larges marges de reconception du noyau, pour optimiser à la fois la géométrie de refroidissement ainsi que la fabricabilité de l’aubage final.
Une opportunité pour les forces? Une menace pour le business model ?
La fabrication additive, procédé « fail fast » par excellence, permet d’envisager à terme la production d’aubes de turbine plus complexes avec un taux de rebut maîtrisé. Mais si elle n’est ici qu’une étape intermédiaire d’un procédé global, la montée en maturité des techniques de fabrication additive, notamment métallique, pourrait constituer à l’avenir une véritable révolution pour le MCO sur base mais aussi en OPEX. La réparation rapide de pièces permettrait une augmentation significative de la disponibilité du matériel, ainsi que des économies substantielles.
Les principaux bénéficiaires de ce saut technologique seraient indéniablement les forces françaises ou étrangères équipées par des industriels français, poussant ces derniers à revoir leurs business models. Le marché des pièces militaires, comme civiles, est menacé : si la certification confère une protection relative, les agences de régulation peuvent par exemple accorder un agrément de fourniture de pièces de rechange.
Comme souvent dans l’aéronautique, la clé du succès viendra des matériaux, aux propriétés spécifiques pour l’impression 3D : céramique photosensible, poudre métallique précisément calibrée... Pour rester dans la course, les grands industriels devront se les approprier au plus vite, en coordination avec l’évolution de leurs matériaux traditionnels. Safran et ses partenaires, comme l’ONERA, y travaillent déjà, avec le SCAF en ligne de mire. Nul doute qu’avec les moteurs de demain fabriqués grâce à une telle technologie, les anglo-saxons n’auront plus l’occasion d’oublier le savoir-faire français en la matière !
![]() |
Thomas Flamme, IA, Architecture moteur M88, DGA
Précédemment en affectation temporaire à la Plate-forme Aubes de Turbine Avancées de Safran Tech, Thomas Flamme a participé à la conception et à l’optimisation thermomécanique des aubes de turbine nouvelle génération dans le cadre du PEA TURENNE. Il est maintenant chargé des activités de suivi en service et de développement du moteur M88 du Rafale, ainsi que des études amont pour les motorisations futures de l’aviation de combat.
|
Ming Long, IA, ingénieur simulation des procédés chez Safran Tech
Actuellement en affectation temporaire à la Plate-forme Aubes de Turbine Avancées de Safran Tech en qualité d’ingénieur, Ming Long participe au développement de nouvelles techniques de simulation, d’optimisation des plans d’essais de fabrication et d’intégration des aspects de fabricabilité lors de la conception d’aubes de turbine nouvelle génération dans le cadre du PEA TURENNE.
|
Aucun commentaire
Vous devez être connecté pour laisser un commentaire. Connectez-vous.